Enhancing Accuracy: The Power of Silicone Rubber Tubes in High-Efficiency Applications
The modern-day industrial landscape is a complex tapestry of precision, efficiency, and technology. As technology advancements, the demand for materials that can stand up to extreme problems, all the while keeping their useful honesty, has never been greater. For engineers and producers participated in high-efficiency applications, silicone rubber tubes have climbed to prestige as a cornerstone of product layout and development, using a functional solution to a selection of obstacles.
From microwave treating to water pipe engineering, silicone rubber tubes provide a perfect equilibrium of strength and adaptability, important for applications in aerospace, health care, and the vehicle markets, to name a few. This article dives deep right into the textile of silicone rubber tubes, uncovering just how variants in product and production can accommodate one of the most intricate demands of modern sector.
Browsing the World of Microwave Treating Silicone Rubbers
In the realm of fast curing procedures, microwave innovation has actually arised as a game-changer, and silicone rubber plays an essential role. Microwave healing silicone rubber tubes supply unequaled speed and performance, drastically lowering production times contrasted to standard techniques. Microwave power upsets the molecular framework of the silicone, increasing the cross-linking process and causing a remarkable, heat-resistant item.
For markets concentrated on high-volume output, such as electronic devices and telecommunications, microwave healing silicone rubber tubes supply a crucial advantage. The high dielectric strength and thermal security of these tubes make certain longevity sought after electrical applications. With reduced energy usage and cycle times, makers can optimize their assembly line for peak efficiency without endangering on top quality.
The Advantages of Fluorosilicone Rubber for Flexible Tubes Solutions
Versatile tubing is a foundation of lots of intricate systems, specifically those that enter call with severe chemicals or extreme temperature levels. Fluorosilicone rubber stands out as a specialized material recognized for its phenomenal resistance to fuels, oils, and solvents. This makes it a perfect prospect for applications such as fuel lines, hydraulic systems, and within the aquatic industry.
The versatility of fluorosilicone rubber makes sure that flexible tubes keeps its architectural stability over time, even when revealed to one of the most aggressive settings. Its reduced compression set residential or commercial properties and capability to keep versatility across a wide temperature variety guarantee constant efficiency, making it a dependable service for high-efficiency systems that can not afford downtime.
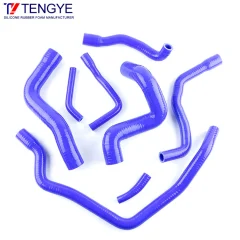
Tailoring Silicone Rubber Tubes for Non-Porous Applications
In industries where contamination is not a choice, the non-porous nature of silicone rubber tubes is an important function. In health care, drugs, and food processing, the highest degree of hygiene and item purity have to be preserved. Silicone rubber succeeds in these sectors, as its safe, non-stick qualities make it the material of selection for non-porous tube options.
Accuracy extrusion methods allow makers to produce silicone rubber tubes with smooth, glass-like surfaces that prevent the development of germs and protect against contamination. Whether promoting the transfer of essential liquids or playing a function in product packaging, these tubes are a vital component for ensuring high quality and safety and security in high-efficiency applications.
Leveraging Thermoplastic Resins for Improved Tube Shrinkage
Thermoplastic materials are a flexible team of products that, when combined with silicone rubber, can produce tubes with one-of-a-kind residential or commercial properties. Among one of the most compelling attributes is the capacity to produce silicone rubber tubes with controlled shrinking. This can be essential in applications where a safe, tight-sealing fit is essential to protect against leaks or make sure insulation.
As an example, in the vehicle industry, silicone rubber tubes with controlled contraction are extensively made use of for cable and cord harnessing. By carefully adjusting the extrusion procedure, suppliers can determine the last size and wall thickness of televisions, using customized remedies for different components and systems within automobiles.
Cutting-Edge Processes for Manufacturing Silicone Water Pipes
Pipes are important parts across numerous markets, from residential plumbing to commercial flow systems. Silicone rubber water pipelines provide an engaging alternative to typical materials like PVC or copper. Silicone's resistance to scaling and deterioration, integrated with its pliability and convenience of installation, make it a durable and effective service for water management systems.
Advanced producing processes, such as 3D printing and precision molding, have moved silicone pipes right into the future. These strategies permit the creation of complex forms and designs that satisfy particular flow needs, whether in a family faucet or a large commercial air conditioning system. With innovations in silicone formulations, pipes now can provide not just water, but additionally enhanced sturdiness and long life.
https://www.tengyexc.com/products/ via the world of silicone rubber tubes is among resourcefulness and constant innovation. From their duties in essential applications to pioneering production procedures, the versatility and strength of silicone rubber tubes make them indispensable in our quest for high-efficiency systems and services. As we advance, it's clear that silicone rubber innovation will certainly continue to play a leading role in shaping the commercial landscape of tomorrow.