Making The Most Of Force: Comprehending Linearly Applied Power in Marking Presses
As commercial production proceeds to develop, one continuous remains: the vital role of force in forming raw products into precision parts. In modern-day stamping presses, the manner in which force is used works as a silent yet stalwart driver of performance and quality. This guide studies the nuanced world of linearly used power, exploring its effect on marking press procedures and the considerations vital to integrating such modern technology.
The Design Behind Linearly Applied Forces in Industrial Presses
Stamping presses are veritable giants in the manufacturing facility globe-- substantial, effective equipments made to change sheet steel right into a magnificent selection of items. The straight application of pressure is an innovative technique that stands in plain contrast to conventional, eccentrically-loaded press designs. In a linear press, a balanced pressure is used directly over the center of the slide, leading to more constant component measurements and boosted pass away life. This nuanced design isn't merely concerning putting the force in a different area; it's the dish for press procedures that can be likened to a Swiss watch-- detailed and specific.
The Advantages of Linear Over Unusual Presses
The advantages of linear pressure do not start and finish with marking precision. A linear press design likewise significantly decreases the twisting and off-center lots that frequently torment eccentric presses, leading to improved security and much less deterioration on the machine. Furthermore, direct presses frequently boast greater regularities and enable an extra reliable feed setup, which is crucial for producers that require high-volume manufacturing without endangering accuracy.
grinding wheel -Dive into the Mechanical Setup
Tipping into the heart of the equipment, a direct press's mechanical setup is a wonder. The crucial elements adding to this system contain a slide that goes up and down in a straight movement, a press bed that sustains the product to be marked, and a collection of guide articles and bearings that preserve the placement and smoothness of the slide's activity. This direct, direct mechanical configuration disperses energy better, leading to very little energy loss and a plain improvement in press efficiency.
How Straight Application of Force Improves Stamping Press Outcomes
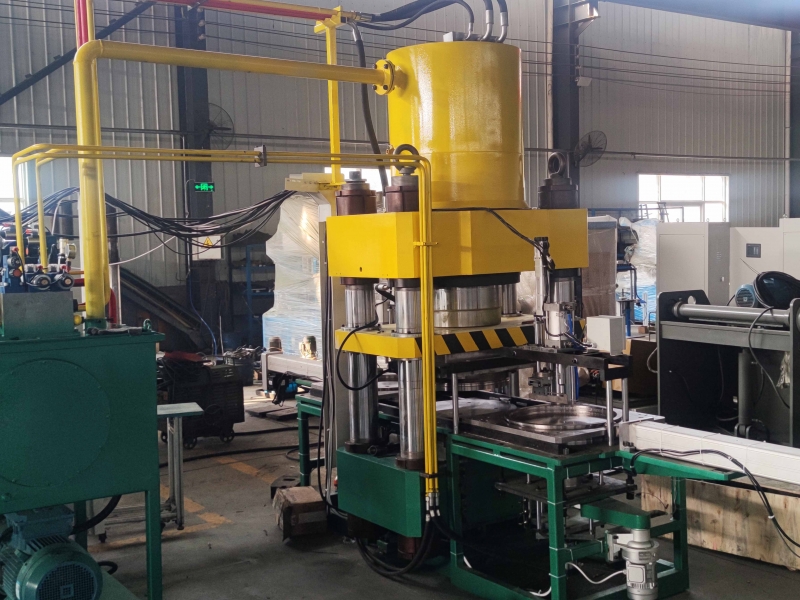
With greater understanding right into the technological specifics of straight pressure application, it's critical to recognize how this layout aspect straight affects the outcomes of the stamping process.
Precision That is Greater Than Skin Deep
In the realm of item quality, precision is paramount. A linear application of force makes certain that the whole die cavity is loaded consistently, minimizing the need for secondary operations and improving total part honesty. The predictable and constant pressure transfer leads to stamped parts with tight tolerances and crisp geometries that meet even one of the most stringent high quality standards.
The Quiet Champion of Pass Away Use
With each successive marking operation, the dies within a press go through put on. The uniformity supplied by straight pressure implies that, unlike in eccentric presses that experience pressure spikes, die wear in straight systems is relatively uniform. This extensive die life converts to guide and considerable price financial savings for producers, as dies are both expensive to produce and change.
Upgrading to a Linearly Applied Force Mechanism: What You Need to Know
Choosing to transition to a linear press is a substantial step for any type of manufacturing procedure. It notes a commitment to sophisticated innovation and a recognition of the value that linear pressure application brings to stamping processes.
Picking the Right Press for Your Application
The journey to a direct marking press starts with an essential analysis of your production demands. Different presses accommodate numerous products and component geometries, and it is important to pick one that aligns with your specific production requirements. From the dimension of the press to the force capability, each information influences the performance and performance of the maker in your distinct manufacturing atmosphere.
Incorporating Linear Push Into Your Stamping Processes
Incorporating a direct press right into your current stamping process needs a keen understanding of your existing procedure. Everything from the installation site to material handling approaches needs to be reviewed and possibly gotten used to guarantee a smooth transition. Operators likewise require to be re-trained to fully utilize on the innovative capabilities that a direct press deals.
Calculating the ROI on Stamping Presses with Linearly Applied Pressure
The switch to a linear press is not just a technical innovation-- it is a tactical service action. Recognizing the roi (ROI) of this change is crucial for assessing its long-lasting viability and advantages.
The Substantial and Abstract Returns
Quantifiable financial savings in material and energy are the very first line of defense in warranting the investment in a linear press. Nevertheless, the lasting advantages, such as increased client fulfillment and enhanced market competition as a result of better components, are just as important. Executing a linear press prolongs beyond an ROI estimation; it's around future-proofing procedures and placing for continual success.
ROI Structures and Metrics
Different structures and metrics can aid evaluate the financial effect of a direct press, from basic repayment durations to more intricate discounted capital analysis. Leveraging these devices offers an extensive understanding of the financial implications and help in strategic decision-making.
Troubleshooting Common Issues in Presses with Linear Force Application
Even one of the most advanced equipment is not unsusceptible to issues. Determining and attending to prospective issues with a linear press is a proactive action that makes sure constant manufacturing and minimal downtime.
Comprehending the Composition of Maker Break Downs
Failures can be identified into different groups-- mechanical, electric, and fluid power. grinding wheel detailed understanding of your press's parts and their communications is indispensable when diagnosing the source of a trouble. Routine upkeep and examinations are vital in protecting against most of these concerns before they take place.
Accepting a Culture of Continuous Enhancement
Proactive troubleshooting is just one aspect of a wider dedication to continuous renovation. Urging responses from operators and buying their training grows a society where the cumulative expertise and experience add to refining processes and solving obstacles.
As markets press the boundaries of what is feasible in manufacturing, straight application of pressure arises as a key enabler of precision and performance. This change in the mechanics of marking presses represents not simply an engineering feat, yet a tactical state of mind that accepts the future of production. Embracing this change is a financial investment in the quality and success of your manufacturing efforts-- a testimony to the effective influence of a linearly applied force.