Recognizing Automatic Control Valves: Fundamentals to Advanced Applications
In the domain of liquid control, Automatic Control Valves stand for a peak of accuracy design and play an indispensable duty in a myriad of commercial, community, and business settings. From preserving ideal stress, circulation, and level in pipelines to regulating process variables in chemical plants and a/c systems, automated valves are prevalent. This extensive guide will certainly walk you through the important aspects, from the fundamentals to innovative choice and upkeep of automatic control shutoffs, providing you the understanding to make enlightened decisions for your projects.
What Is an Automatic Control Valve and Exactly How Does It Function?
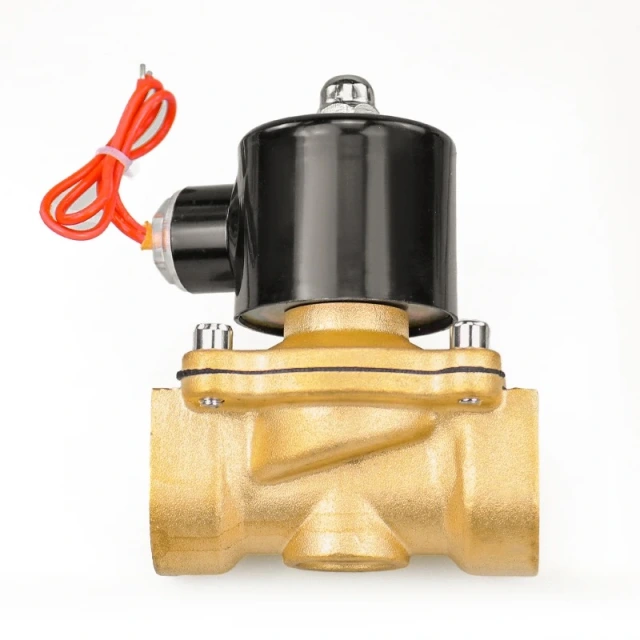
Automatic Control Valves (ACVs) are vital components of automated control systems, tasked with taking care of the circulation, stress, and fluid degrees in different operational atmospheres. They attain this via a combination of sensors, actuators, and a carefully made valve body that can regulate and keep the preferred circulation characteristics under dynamic conditions.
At the heart of an ACV is the actuator, which is the muscle mass relocating the shutoff stem to open or shut the pathway for fluid. This actuator can be managed by a series of systems, consisting of pneumatically-driven, hydraulic, and electronic controllers. The shutoff's body is crafted to reduce cavitation, decrease pressure decline, and improve control precision.
The principles behind automated control shutoffs involve a proportional-integral-derivative (PID) control loophole. Sensors determine the process variable (e.g., stress or circulation rate), which is after that contrasted to the preferred setpoint. The controller determines the mistake and adjusts the actuator accordingly to remedy the discrepancy, guaranteeing the process continues to be within the defined limitations.
The Evolution of Automatic Control Valves in Industrial Applications
Over the years, the evolution of automatic valves has actually been noted by significant technological developments. Conventional world valves with manual adjustment found in very early commercial setups were rapidly changed by diaphragm- and piston-operated automatic valves, which brought in higher performance and reliability.
With boosted automation and digitalization, contemporary ACVs are incorporated right into complex control networks, interacting information back to central systems and enabling remote monitoring and modification. Their role in essential framework such as water treatment plants, power generation facilities, and oil refineries can not be overstated.
In today's digitally linked world, the growth of wise shutoffs has even more changed the landscape. These valves use advanced sensors and onboard microprocessors to improve the control process, anticipate maintenance needs, and adapt to transforming operational problems more efficiently.
Comparing Pneumatically-driven, Hydraulic, and Electric Automatic Valves
When choosing an automatic valve, among the key considerations is the sort of actuation system it uses: pneumatic, hydraulic, or electric. Each has its own collection of merits, and the selection depends upon aspects such as the application, setting, and control needs.
Pneumatically-driven shutoffs, powered by compressed air, are recognized for their rapid action times and are typically made use of in high-paced manufacturing procedures where fast actuation is important. water solenoid valve are liked for their high force-to-size ratio, making them suitable for heavy-duty applications such as earthmoving tools and big machinery.
Electric automatic shutoffs, on the various other hand, have actually made significant invasions because of their precision and controllability. With the improvements in electric actuator technology, they can currently compete toe-to-toe with pneumatically-driven and hydraulic alternatives. Electric shutoffs provide the advantage of being energy effective, less complicated to maintain, and extra fit for usage in clean-room applications where air or hydraulic liquid contamination is a problem.
Selecting the Right Automatic Control Shutoff for Your Task
The effective application of automatic control valves hinges on choosing the appropriate type, size, and material for the task. Sizing the shutoff appropriately is important to guarantee it can manage the expected flow prices without excess stress decrease or cavitation, which causes erosion and early failing.
Product option is equally important. Valves might need to withstand destructive chemicals, heats, or unpleasant fluids. Usual products include stainless steel for exceptional deterioration resistance, bronze for drinkable water applications, and different crafted plastics.
Other factors to consider are the control characteristics of the valve, such as linear, equivalent portion, or quick opening, which impact how the valve reacts to modifications in actuation. Ultimately, combination right into the existing control system and the called for certifications for safety and performance standards ought to also be considered.
A Study in Shutoff Option
Picture a circumstance where a community requires to upgrade the control valves in its water circulation system to boost performance and lower water losses. The design group would first require to examine the operating problems and circulation patterns throughout the network to recognize crucial points where automatic control valves are essential.
For https://wenhuivalve.com/blog-detail/understanding-automatic-control-valves-basics-to-advanced-applications , they could choose electrical automated control valves for their exact control capacities and compatibility with the information purchase system. Sizing the valves based upon peak demand and stress requirements will be crucial to stop over- or under-sizing. Materials would certainly be chosen based upon the water top quality parameters, with considerations for drinkable water standards and long-term reliability.
The chosen valves would certainly then require to reveal conformity with sector guidelines and criteria, and their installment would certainly be come with by a carefully developed upkeep strategy to make certain regular performance.
Upkeep Tips for Long-Term Dependability of Automatic Control Valves
Correct maintenance is the cornerstone of expanding the life and efficiency of automatic control valves. Depending upon the type of shutoff and the application, normal maintenance can range from basic examinations to much more in-depth maintenance.
Some common maintenance methods for ACVs include:
Routine calibration and testing of the actuators to ensure they react accurately to regulate signals.
Assessment of the valve body and cut for indicators of wear or damages, which can affect securing and bring about leaks.
Lubrication of relocating parts for pneumatically-driven and hydraulic shutoffs to preserve smooth operation.
Looking for air or liquid leaks that can compromise the actuator's efficiency.
Routine substitute of wearing parts, such as seals and gaskets, to avoid unforeseen failures.
By adhering to a structured upkeep schedule and immediately resolving any type of issues that emerge, organizations can guarantee the continual and dependable operation of their automated control shutoffs.
Seeking to the Future of Automatic Control Valves
The development of automated control shutoffs is far from over. With the advent of Industry 4.0 and the Net of Points (IoT), we are entering a period where valves are not just easy control gadgets but active individuals in the optimization of commercial procedures.
In the coming years, we can anticipate to see more integration of ACVs right into clever, interconnected systems that boost power efficiency, reduce downtime, and give unprecedented levels of control and automation. The possibility for advancement in this room is large, and automated control valves will remain to be at the leading edge of liquid control technology.