Understanding Automatic Control Valves: Essentials to Advanced Applications
In the domain name of fluid control, Automatic Control Valves stand for a peak of accuracy engineering and play a vital duty in a myriad of commercial, metropolitan, and commercial setups. From preserving ideal stress, flow, and degree in pipelines to managing process variables in chemical plants and a/c systems, automated valves are prevalent. This detailed overview will certainly walk you via the important facets, from the basics to advanced choice and maintenance of automatic control valves, giving you the understanding to make educated choices for your tasks.
What Is an Automatic Control Valve and How Does It Function?
Automatic Control Valves (ACVs) are key elements of automated control systems, tasked with handling the flow, pressure, and liquid levels in different functional environments. They attain this through a mix of sensing units, actuators, and a very carefully developed valve body that can modulate and keep the desired flow attributes under dynamic problems.
At the heart of an ACV is the actuator, which is the muscle mass moving the shutoff stem to open or close the pathway for fluid. This actuator can be managed by a series of systems, consisting of pneumatic, hydraulic, and digital controllers. The valve's body is crafted to minimize cavitation, lower stress decrease, and boost control accuracy.
The principles behind automated control shutoffs entail a proportional-integral-derivative (PID) control loophole. Sensing units determine the procedure variable (e.g., pressure or flow price), which is then compared to the preferred setpoint. The controller computes the mistake and changes the actuator accordingly to remedy the variance, making certain the process continues to be within the defined limitations.
The Advancement of Automatic Control Valves in Industrial Applications
Over the decades, the development of automated shutoffs has actually been noted by considerable technical developments. Conventional world shutoffs with hand-operated change discovered in very early commercial configurations were swiftly replaced by diaphragm- and piston-operated automated valves, which generated greater functionality and integrity.
With increased automation and digitalization, modern ACVs are incorporated into intricate control networks, communicating information back to central systems and allowing remote surveillance and adjustment. Their duty in important framework such as water therapy plants, power generation centers, and oil refineries can not be overemphasized.
In today's digitally connected globe, the advancement of wise valves has actually further transformed the landscape. These shutoffs utilize innovative sensors and onboard microprocessors to streamline the control procedure, anticipate upkeep needs, and adjust to altering operational problems more successfully.
Comparing Pneumatic, Hydraulic, and Electric Automatic Valves
When selecting an automatic shutoff, one of the primary considerations is the kind of actuation system it utilizes: pneumatically-driven, hydraulic, or electrical. Each has its own collection of benefits, and the choice depends on variables such as the application, environment, and control needs.
Pneumatic valves, powered by pressed air, are known for their fast action times and are typically utilized in high-paced manufacturing processes where fast actuation is crucial. Hydraulic valves are chosen for their high force-to-size proportion, making them appropriate for heavy-duty applications such as earthmoving equipment and huge machinery.
Electric automated shutoffs, on the other hand, have actually made significant inroads due to their accuracy and controllability. With the developments in electrical actuator technology, they can now compete toe-to-toe with pneumatically-driven and hydraulic alternatives. Electric shutoffs use the benefit of being power efficient, less complicated to maintain, and more matched for usage in clean-room applications where air or hydraulic liquid contamination is a problem.
Selecting the Right Automatic Control Valve for Your Job
The effective application of automated control valves depends upon choosing the ideal kind, size, and material for the task. Sizing the shutoff correctly is crucial to guarantee it can handle the expected flow rates without excess stress decline or cavitation, which causes erosion and premature failing.
Material selection is just as vital. Shutoffs may need to hold up against harsh chemicals, heats, or rough fluids. Common materials include stainless steel for superb rust resistance, bronze for safe and clean water applications, and numerous engineered plastics.
Other variables to think about are the control qualities of the shutoff, such as direct, equivalent percent, or fast opening, which influence exactly how the valve replies to adjustments in actuation. Ultimately, integration right into the existing control system and the called for qualifications for safety and efficiency criteria ought to also be taken into consideration.
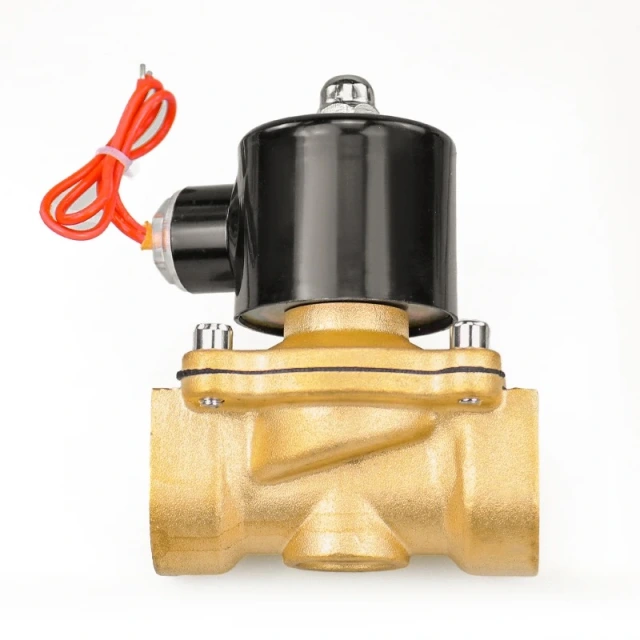
A Situation Research Study in Valve Selection
Envision a scenario where a community needs to update the control shutoffs in its water distribution system to improve efficiency and decrease water losses. The design team would certainly initially need to analyze the operating problems and circulation patterns throughout the network to recognize important factors where automatic control valves are essential.
For this application, they could pick electric automated control valves for their accurate control capabilities and compatibility with the data acquisition system. Sizing the shutoffs based on peak demand and pressure demands will certainly be important to protect against over- or under-sizing. Materials would certainly be selected based upon the water top quality parameters, with factors to consider for drinkable water criteria and long-lasting reliability.
The chosen shutoffs would certainly after that require to show compliance with sector regulations and criteria, and their setup would be accompanied by a very carefully made maintenance strategy to make certain continuous efficiency.
Maintenance Tips for Long-Term Dependability of Automatic Control Valves
Proper upkeep is the cornerstone of prolonging the life and efficiency of automated control valves. Depending upon the sort of shutoff and the application, normal upkeep can range from standard evaluations to a lot more thorough servicing.
Some usual upkeep techniques for ACVs include:
Routine calibration and testing of the actuators to guarantee they respond properly to control signals.
Evaluation of the shutoff body and trim for indications of wear or damages, which can impact securing and result in leakages.
Lubrication of relocating components for pneumatic and hydraulic valves to maintain smooth operation.
Examining for https://www.wenhuivalve.com/products/2w-series or liquid leaks that can jeopardize the actuator's performance.
Routine substitute of putting on components, such as seals and gaskets, to stop unforeseen failings.
By sticking to an organized upkeep schedule and without delay dealing with any type of issues that emerge, organizations can make sure the continuous and trusted operation of their automatic control valves.
Seeking to normally closed solenoid valve of Automatic Control Valves
The evolution of automated control valves is far from over. With the arrival of Industry 4.0 and the Web of Points (IoT), we are entering an age where shutoffs are not simply passive control gadgets but active individuals in the optimization of commercial procedures.
In the coming years, we can expect to see further integration of ACVs right into smart, interconnected systems that boost energy effectiveness, minimize downtime, and provide unprecedented degrees of control and automation. The capacity for technology in this area is huge, and automatic control valves will certainly proceed to be at the center of fluid control innovation.